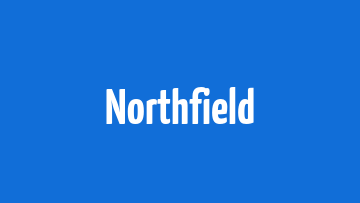
Precision Workholding Chucks: Exploring Collet Chucks, when and how to use them.
Introduction
In the world of manufacturing, precision is not just a desirable quality; it's an absolute necessity. One of the key components that contribute to precision machining is workholding chucks, and among them, collet chucks stand out for their efficiency and versatility. In this article, we'll dive into the world of collet chucks and explore why they are a vital tool for achieving precision in manufacturing processes.
Understanding Collet Chucks
Collet chucks are specialized workholding devices designed to secure and center a workpiece for machining, grinding, or any operation that requires high accuracy and repeatability. They consist of a cylindrical sleeve with a conical inner surface, a collet (a clamping device), and a collet nut. The collet is inserted into the sleeve and is then drawn into the collet nut, creating a strong and concentric grip on the workpiece.
The Use of Collet Chucks
Collet chucks find applications in various industries, including automotive, aerospace, medical, and electronics manufacturing, where precision is paramount. Here's how you can utilize collet chucks:
- Turning and Milling: Collet chucks are commonly used on lathes and milling machines to securely hold cylindrical workpieces like rods and shafts. The collet's uniform grip prevents slippage and ensures concentricity, resulting in precise machining.
- High-Speed Machining: For high-speed machining, collet chucks are indispensable. They reduce vibration and runout, allowing for smoother, more efficient cutting at increased speeds without sacrificing precision.
- Tool Changes: Collet chucks simplify tool changes, making them quicker and more convenient. This feature is particularly valuable when working on complex, multi-step machining tasks.
- Swiss-Style Machining: In precision manufacturing, Swiss-style lathes are often used to produce small, intricate parts. Collet chucks excel in this context, providing the stability and precision needed for micro-machining.
Key Features of Collet Chucks
- Material Compatibility: Collet chucks are available in a variety of materials to suit specific applications. Engineers should choose the material that offers the best combination of rigidity, durability, and corrosion resistance.
- Collet Type: Collet chucks come in different collet types, including standard, step, and emergency collets. The choice depends on the workpiece's shape and size.
- Runout Control: Collet chucks are known for their exceptional runout control, ensuring that the workpiece runs true and concentric to the chuck's axis.
Benefits of Using Collet Chucks
- Enhanced Precision: Collet chucks offer superior concentricity and minimal runout, resulting in precise machining operations and reduced scrap rates.
- Improved Productivity: Quick and reliable tool changes, as well as high-speed machining capabilities, boost productivity and efficiency.
- Cost Savings: Reduced scrap, longer tool life, and minimized machine downtime contribute to cost savings over time.
- Versatility: Collet chucks can accommodate a wide range of workpiece sizes and shapes, making them versatile tools for engineers working on diverse projects.
Summary
For precision workholding solutions, collet chucks are indispensable tools. Their use, along with an understanding of their features and benefits, can significantly contribute to achieving the high levels of accuracy and productivity required in today's competitive manufacturing landscape. By harnessing the capabilities of collet chucks, engineers can take a significant step toward mastering the art of precision machining.