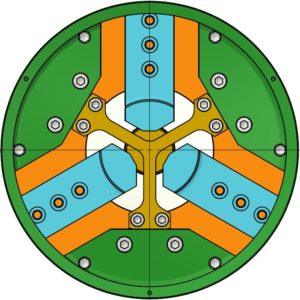
Autonomous Automotive Inspection Workholding
This project is for a longstanding customer who produces: precision machines, tools, and rotary tables. The brief requires gripping the inner diameters of continuously variable transmission (CVT) sheaves for runout inspection.
The Challenge
The work holding challenge is to create a chuck for auto-loading in an autonomous machining environment. We are their preferred supplier for custom and high precision projects and therefore need to deliver our trademark accuracy and repeatability.
Solution: How did we deliver?
Positioning the part by robotic arm requires every custom feature ensures proper seating before the machining operation begins.
Runout Inspection Chuck Drawing - Northfield Proprietary[/caption]
Custom Northfield Precision Model 625 Sliding-Jaw Air Chuck (0.0001” TIR) with special top tooling[/caption]
- The custom top-jaws are permanently mounted onto the chuck’s master-jaws. This grips the inner diameter of the sheave’s central bore.
- The 3 air holes in the top surface of each custom jaw are an air-detect Axial Locator.
- The jaws are also ground at mid-stroke of the chuck, providing a large part-load clearance.
Finally, analysing all critical surfaces that interface with the part, this work holding chuck delivers the trademark Northfield accuracy of of .0001” TIR and repeatability.
Our innovation and relationship building is what sets us apart from the competition. Do you have a high precision challenge? Contact us to see how the Northfield team can solve it.