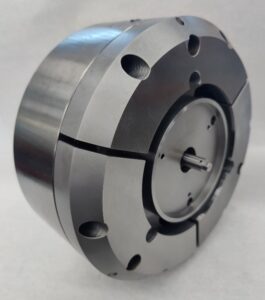
Graphite Ring - Custom Workholding
Introduction
Discover how the Northfield Precision Model 1000W Sliding-Jaw custom workholding Air Chuck is transforming our customer's machining operations. This advanced chuck is equipped with specialized cooling modifications. It addresses the challenges faced by our customer in machining ring shaped parts, gripped by their inner diameter.
Brief
Our customer requires a customised workholding chuck that completes the second stage of their machining process. In the case of the Northfield Precision Model 1000W Sliding-Jaw Air Chuck featured here, there are several customer requirements that we will be addressing:
- Accuracy
- Chip Evacuation
- Thermal Management
- Part Positioning
Precision machining demands meticulous attention to detail. Especially when dealing with intricate parts with tight tolerances. Challenges such as chip evacuation, thermal management, and consistent part positioning can significantly impact machining accuracy and efficiency. Traditional off-the-shelf workholding solutions often fall short in addressing these specific challenges. Leading to compromised quality and increased production costs.
[caption id="attachment_22635" align="aligncenter" width="265"] Murata 1000W Air Chuck[/caption]
Northfield Precision Custom Workholding Solution
The Northfield Precision Model 1000W Sliding-Jaw Air Chuck offers a custom workholding solution to the challenges encountered in precision machining. With customized coolant delivery systems, interchangeable nozzles, and full-face-contact Axial Locators, this advanced chuck is engineered to optimize performance for specific machining applications. The integration of these features ensures efficient chip evacuation, precise thermal management, and consistent part positioning, guaranteeing superior machining accuracy and repeatability.
- Accuracy: The customer demanded a high level of precision, with tolerances as tight as 0.0001” TIR across critical surfaces. Achieving this level of accuracy required meticulous design. Ensuring every aspect of the chuck met the stringent requirements.
- Chip Evacuation: The customer requested a customized coolant delivery system to effectively evacuate chips and keep the cutting tool cool during machining. Efficient chip evacuation was crucial for two reasons: maintaining a clean cutting environment and preventing chip build-up that could affect accuracy.
- Thermal Management: To prevent heat-induced dimensional inaccuracies and to prolong tool life, the customer required a solution that could effectively manage temperatures during machining. The customized coolant delivery system ensures consistent performance throughout the machining process.
- Part Positioning: Consistent part positioning was essential to achieving accurate machining results. The inclusion of a full-face-contact Axial Locator ensured that the part would sit on its high spots when loaded into the chuck. Therefore, providing optimal contact between the workpiece and the chuck face.
[caption id="attachment_22634" align="aligncenter" width="279"] Murata 1000W Air Chuck Close-up[/caption]
Custom Workholding Results
By investing in a custom workholding solution our customer is achieving unparalleled precision and efficiency in their machining operations.
This custom Northfield solution has:
- Ability to maintain accuracy within 0.0001” TIR
- Accommodate a wide range of part geometries
- Seamless transition between machining stages
- Ensures the highest quality output
The result is improved productivity, reduced setup times, and increased profitability.
Ready to elevate your precision machining capabilities with custom workholding solutions from Northfield Precision? Our team of experts is here to assist you every step of the way.
Reach out to us via phone, email, or through our online contact form to get started. Let's work together to achieve precision.
https://northfieldog.wpenginepowered.com/contact/